KABAN MD 3020
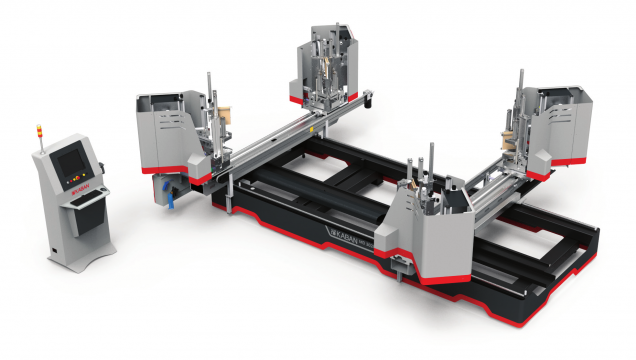
KABAN MD 3020 - KABAN - KABAN MD 3020
General Features
• It welds the four corners of the PVC profiles without any chips at an angle of 90 °. In the first stage, the welding surface areas of the profiles placed on the machine are milled with the help of the milling group consisting of cutting tips. After milling, the profiles are welded at a 90 ° angle. Finally, the stripping blades remove the weld chips.
• With PID system, heating degree and time parameters are set independently from each other.
• A smooth gasket assembly is achieved without using a gasket system.
• Thanks to the teflon renewal system in roll form in the resistance plate, it distributes heat homogeneously and saves time and cost.
• Time saving thanks to practical welding mould replacement system.
• Thanks to the functional program, it provides separate adjustment for each edge in milling operations.
• It tolerates cutting angle errors in profiles up to 0.5 °.
• It tolerates cutting length errors in the profiles up to +2 mm.
• It is positioned according to the profile size and provides easy profile placement of the operator.
• It provides easy control thanks to digital control system in all axes.
• It is possible to make measure tolerance in all axes separately.
• The pressure control system allows the machine to operate at the correct air pressure.
• Automatic lubrication system.
• Computer controlled axial movements ensure a measurement accuracy of less than 0.1 mm.
• Easy operation and programming with 17” LCD Monitor.
• It is possible to define a separate process at every point via the profile drawing in DXF format.
• It makes welding without any chips on the outer surfaces by means of our own system. Therefore, it does not require corner cleaning after welding.
• Less space than the current welding and cleaning center.
• Saves workforce as it works with a single operator.
• It can be used with PVC profiles of all colors.
Milling
• The milling group consists of cutting tips and makes the milling of profile surface and gasket to be welded.
Operation System
• Easy to use and flexible operating system works with all joinery and optimization programs.
• By means of special software, the stowing order in the profile trolley can be selected from the screen and customer based production can be made.
• Easy parameter setting.
• Periodic maintenance reminder function is available.
• Welding can be done by entering manual measurement without using barcode reader.
• Barcode reader is included.
• Ethernet connection.
Welding Moulds
• Time saving thanks to practical welding mould replacement system.
• Axes can be positioned with a precision of 0.1mm.
• Cutting and welding tolerances are distributed evenly to 4 corners.
• X and Y axes are positioned automatically.
Stripping Blade
• Stripping blades remove the chips caused by welding process on the upper and lower surfaces of the profile.
Heating Plate
• Heating plates provide uniform distribution of heat. With the special teflon system on these plates, longer term and more efficient teflon usage is provided. Teflon replacement system in the form of rolls saves time and cost.
Electricity:
Operating voltage 400V, L1-L2-L3-N-PE, 50/60 Hz
Total power 28.25 kW
Air pressure: 6-8 Bar
Air consumption: 80 Lit / cycle
Machine Dimensions:
Width (W) 7250 mm
Height (H) 2010 mm
Length (L) 5190 mm
Weight: 2210 kg
WELDABLE AND CLEANABLE
Profile Dimensions
- Frame size (AxB):
Min 420 x 385 mm
Max 4125 x 2500 mm
- Profile size:
(a) Max 140 mm
(h) Min 20 mm
(h) Max 190 mm
Screen: 17 “LCD
Software:
Kaban Transfer Windows (optional)